Facility Inspections
For 30 years our customers have come to depend on Paladin’s certified Inspection Team to keep their systems up and functioning correctly. Our team carries the highest level of licenses and certifications as well as an understanding of all codes. We assist customers with acceptance testing as well as annual, semi-annual, and quarterly inspections, as required by insurance and state and local codes. The Paladin Inspection Team is not limited by manufacturer or facility/project size as we service most major brands.
After years of performing inspections, we have separated ourselves from the rest of the industry. How has our team done this? Through our focus on customer satisfaction. After listening to our customers’ needs and wants, we have developed a program that provides them with one source to manage all of their inspection needs. So, what does this mean to you as a customer? Our customers no longer need to coordinate with multiple inspection contractors to keep facilities current with today’s Life Safety needs. Let us do the heavy lifting as we will monitor your inspections needs and contact you when your inspections are due. During this process, we will coordinate our Inspection Team around your facility’s scheduling requirements. We will also contact your local AHJ (Authority having Jurisdiction) and notify them when the inspection will commence as required by NFPA (National Fire Protection Association).
The separation does not stop there however. In 2016, our President at Paladin implemented a Cloud Based Inspection System called eVance by Honeywell to better serve all of our client’s needs. The implementation of this system eliminates the need to store or file paper copies of inspection results on premise, as you can simply access all of your inspection records in the cloud from anywhere, at any time, via a connected device. The eVance Cloud Based Inspection System contains a list of all inspection points that our Paladin Team needs to “Pass” or “Fail” which reduces the risk of missing critical inspection points during the process.
Let us move your inspection reports into the new age of document recording! Paladin offers all of our customers this web-based inspection reporting option. This system allows our team to customize the inspection reports to meet your specific facility and insurance requirements allowing you to easily keep your reports organized in one location. Our representatives are available to answer any questions that you may have regarding this system.
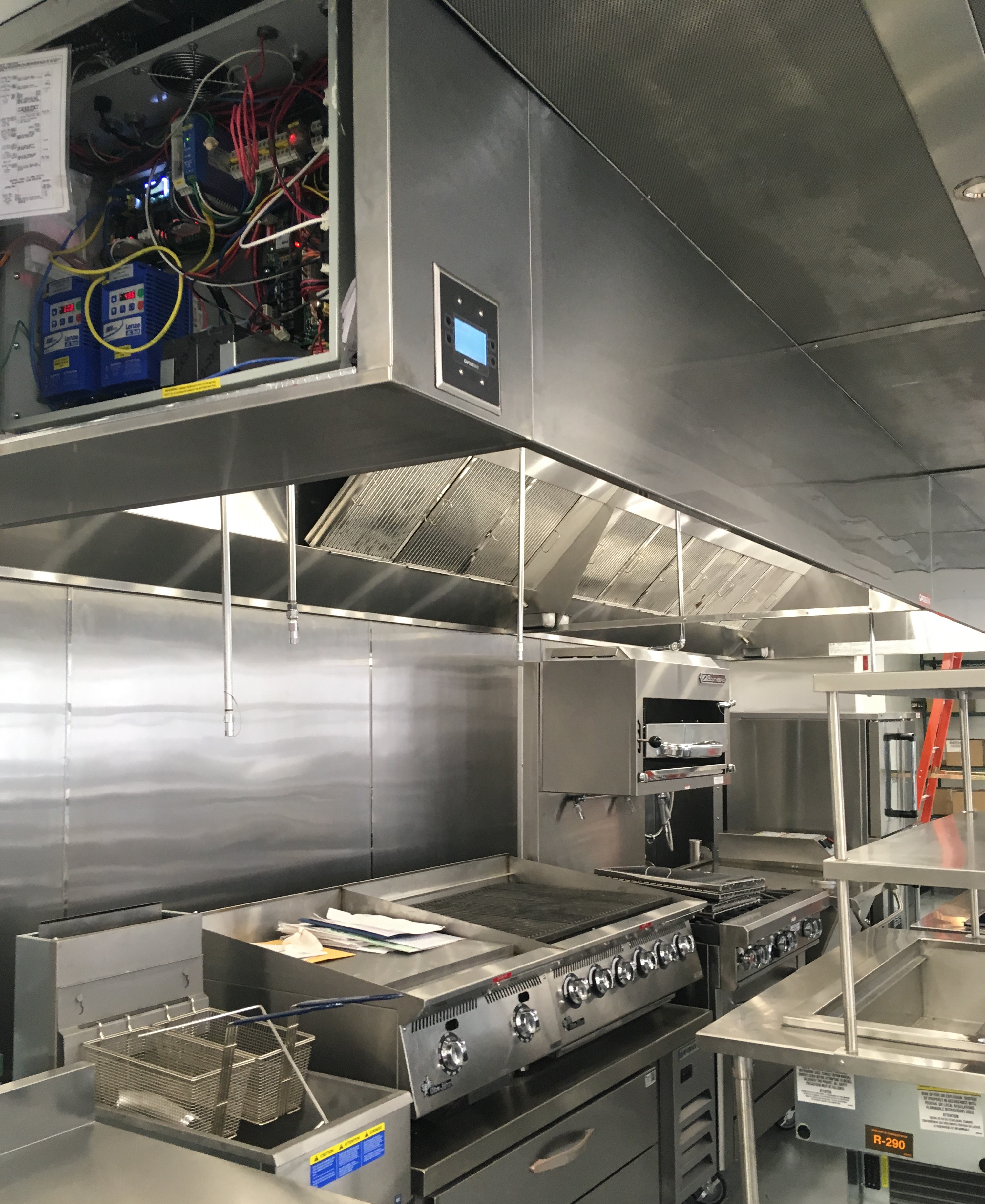
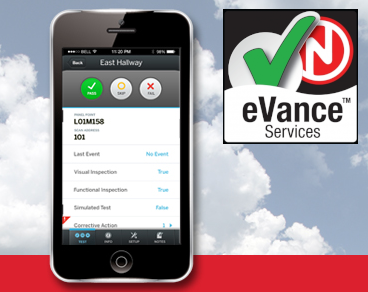
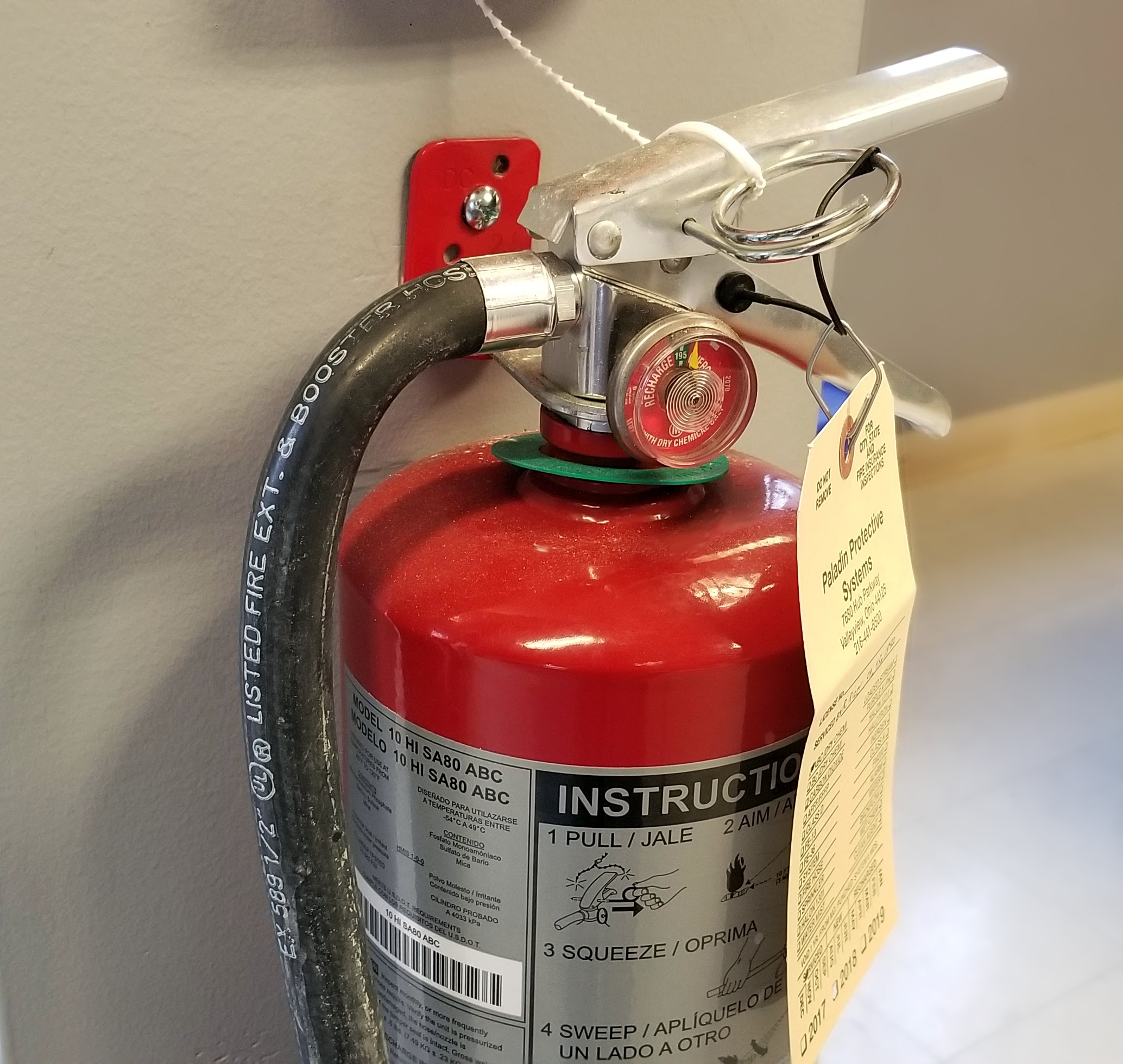
One of Paladin’s core values is “Communication” and our inspection process supports the value to communicate at a high level with our customers on every aspect of their inspections.
Our Team provides the following Inspection Services:
- Fire Alarm System Inspections
- Sprinkler System Inspections
- Fire Extinguisher Inspections
- Emergency Light Inspections
- Kitchen Hood Inspections and Cleaning
- Fire Pump Inspections
- Backflow Prevention Inspections
- Hydrant Inspections
- And More!!
Let Paladin be your “One Source” for all of your inspection needs! Call us today at 800-332-0603 to schedule your next inspection.
Additional Testing Information
Q) How often is a Kitchen Hood Inspection required to be performed?
A) Kitchen Hood Inspections are required semi-annually
Q) What does the Kitchen Hood Inspection cover?
A) Kitchen Hood Inspections consist of checking the following:
- Nozzles are checked
- Heads are checked
- Replace all links
- Check to confirm the system trips
- Check for any corrosion or other damage
- Check CO2 cartridges
A) After the inspection is completed, tags are applied to the system to provide verification of when the Kitchen Hood was inspected and what company provided the inspection. This is required in case your facility is ever inspected by the local Fire Marshall. A report is also generated which indicates all of the results as well as recommendations for any repairs that may be needed.
- Check for visual signs that the system has been fired, tampered with or leaked. Disconnect system for inspection. (Paladin will alert personnel, Central Station Monitoring Center and Fire Department before testing begins.)
- Check the cylinder condition and hydrostatic test date. Check the regulator test date of the system, if applicable.
- Check all piping and conduit to verify they are secure and properly mounted. Verify the pipe and nozzles are free of blockage and properly aimed at appliance surfaces.
- Replace all fusible links. If a system is electrical, test the detectors, the control panels and the battery back-up to ensure proper functionality. (Fusible links should be replaced on a semi-annual basis.)
- Perform a dry test of the system for automatic operation and manual release.
- Check operation of gas shut-off and/or electrical shut-off
- Confirm the fuel shut-off is in the “ON” position. Weigh and replace fire system cartridges as required.
- Check chemical type and quantity.
- Verify the filter type in the Kitchen Hood and proper decals at the remote pull stations are in place.
- Complete the Inspection Report and attach inspection tags. Check for proper type of portable Fire Extinguishers are in the Kitchen area (K Class) and verify they have been properly inspected.
According to the NFPA.org, if a fire is going to start, it’s likely to start in a Kitchen. Don’t let your Kitchen facilities go under-protected from fire. Regular cleaning of Kitchen Hoods is recommended. Keep your employees, customers, visitors and property safe by calling Paladin’s Service Department at 800-332-0603 to arrange an inspection or cleaning of your Kitchen Hood System.
Check Accessibility
- Identify if a Fire Extinguisher is present in the area and take note if it is easily visible.
- It should not be blocked by any equipment or other objects that would make it difficult to be accessed during an emergency.
- Portable Fire Extinguishers, other than wheeled types, must also be secured in a specific location (e.g. inside an unlocked glass cabinet or a wooden box) to prevent them from being moved.
Examine its Physical State
- Look for the Fire Extinguisher’s serial number and check if the Fire Extinguisher label is readable.
- Check if the cylinder and other external metal parts are free of corrosion, dents, and other signs of damage.
- Check the connection between the hose and cylinder is secure.
- Inspect if there are cracks in the hose or leaks in the nozzle.
- Check if the locking pin goes through the holes of discharge lever and handle, and if the pin is secured well by the seal. The pin locks the discharge lever and prevents accidental discharge.
Check the Pressure Gauge
- Examine where the gauge needle is. A needle within the green zone is good. A needle in the left red zone means that the Fire Extinguisher is undercharged and warrants a recharge, while a needle in the right red zone signals a danger of being overcharged.
Update Inspection Tag
- The tag should indicate that a Fire Extinguisher is regularly inspected.
Generate Report and Recommend Action if Needed
- Once an inspection is completed, summarize observations/action plan. Make sure to sign off on the Fire Extinguisher inspection tag (if available) with your name/signature and date of inspection.
Maintenance Schedule
- ABC/BC requires an internal maintenance every 6 years and a hydrostatic test every 12 years from the date that the Fire Extinguisher was manufactured.
- Class K requires a hydrostatic test every 5 years from the date that the Fire Extinguisher was manufactured.
- Halon requires an internal maintenance every 6 years and a hydrostatic test every 12 years from the date that the Fire Extinguisher was manufactured.
- Halotron requires an internal maintenance every 6 years and a hydrostatic test every 12 years from the date that the Fire Extinguisher was manufactured.
- FE-36 requires an internal maintenance every 6 years and a hydrostatic test every 12 years from the date that the Fire Extinguisher was manufactured.
- Co2 requires a hydrostatic test every 5 years from the date that the Fire Extinguisher was manufactured.
- Water requires a hydrostatic test every 5 years from the date that the Fire Extinguisher was manufactured.
**Any time that a Fire Extinguisher has been partially discharged, it needs to be completely recharged.
Top 5 Fire Extinguisher Inspection Issues and Paladin’s Action Plan
Fire Extinguisher location is obstructed
- Plan - Immediately remove the obstructions or repostion the Fire Extinguisher
Cylinder has dents and or rust
- Plan - Retrieve Fire Extinguisher and provide a quote for a replacement
- Plan – Recharge needed regardless of overcharged or undercharged
Missing locking pin/broken tamper seal
- Plan - Immediately get replacements from Paladin
Fire Extinguisher is not elevated from the floor
- Plan - Request a metal bracket where the cylinder can be hung, or a box that can elevate the cylinder above the floor